2014.2 Successful first half year
Editorial
The demand for transport in freight traffic is benefiting from the positive economic development in domestic and international transport. This is what emerges from the current short term forecast for 2014/2015 by the Federal Ministry of Transport and Digital Infrastructure (BMVI). The forecast is that the volume of freight traffic (tonnes) 2014 will rise by 3.5 %, with the volume of road freight growing by around 4.0 %.Good news that we can confirm. For the CargoFamily, the first half of the year was very successful with over 750,000 shipments and a total weight of over 270,000 tonnes – and the second half of the year looks equally promising.
In addition to pure business development, there is also some significant news from the network: our participation in a trucker initiative, a valuable thesis in the VTL system headquarters, and the innovative solution for scheduling and processing of part loads by PLA.
This NewsTrailer also reports on the “Green commitment” by our partners and the new CO2 tool, which automatically creates our shipment tables.
To ensure the further positive development of the VTL network, we are systematically promoting young talent and will continue to employ both former apprentices of the year for 2014, with one of them in dual studies.
I look forward to welcoming you all to our system meeting on the 7th of November 2014 in Bremen.
Yours, Andreas Jäschke
Managing Director VTL Vernetzte-Transport-Logistik GmbH
New CO2 tool deployed
In accordance with the EU-wide uniform standards for determining energy consumption and greenhouse gas emissions for transport services, VTL has automated the calculation of its shipment-specific carbon footprint and had it certified by TÜV Rheinland under DIN EN 16258.
In addition to political pressure and rising energy costs, many shippers are demanding “green products” from their logistics service providers. To meet these growing requirements, VTL has been regularly calculating the footprint for the entire network since 2010, the so-called network carbon footprint (NCF), and providing its partners with shipment-specific CO2 emissions in the form of shipment tables, broken down into weight and distance classes.
After initially working with the DIN EN ISO 14064 standard, VTL decided to move to DIN EN 16258 this year, as the newly developed standard was created specifically for the transport and logistics sector. In comparison to the previous calculation, emissions from handling and administration are not included here.
From September onwards, the CO2 programme table will now be automatically created. This is made possible by a tool developed by SBZ SL (Steinbeis-Beratungszentrum Spedition und Logistik) that has been jointly tailored to VTL’s requirements. The procedure has been certified for the first time under DIN EN 16258:2013-03.
In addition, the database-driven, automated calculation allows the VTL headquarters main run analyses on weight and number of shipments, as well as comparisons with minimum, maximum and average for all partners. The new tool gives the VTL partner depots the chance to take part in benchmarking in local transport – key figures such as stop density, tours length and, for example, consumption are ascertained.
But this is just the beginning; an upgrade with graphical analysis options is planned for 2015. A link to a web portal is also in the planning and in the future this will allow partners to enter their data directly into the tool.
TÜV Rheinland once again certifies Bentheimer Eisenbahn’s corporate carbon footprint

Transport is an increasingly clean issue at Kraftverkehr Emsland (KVE) GmbH. Proof of this is recertification in accordance with the recognised standard DIN EN ISO 14064-1/3. TÜV Rheinland certified the corporate carbon footprint of KVE’s parent company of Bentheimer Eisenbahn AG. The result: compared to the previous year, the North West German transport company was able to reduce its greenhouse gas emissions by 3.83 per cent per thousand Euro of turnover.
Bentheimer Eisenbahn has set itself the goal of minimising negative environmental impacts in all areas of business – and has therefore once again undergone a voluntary and independent audit of the corporate greenhouse gas balance. This involved looking at all directly and indirectly released climate-relevant greenhouse gases of various group companies. These include, in addition to the local rail freight and passenger transport, the Spedition Kraftverkehr Emsland GmbH, the Berndt GmbH travel agency, the Werkstatt Nutzfahrzeuge Nordhorn GmbH and the Euroterminal Coevorden.
Determining the greenhouse gas balance enables Bentheimer Eisenbahn to sustainably reduce their greenhouse gas emissions with appropriate improvement measures and a look at the figures shows that this is working. In 2011 for example, 296.38 kg CO2e released according to the greenhouse gas emissions per thousand Euro of sales certified by TÜV Rheinland. In the currently certified greenhouse gas emission, this value has been reduced to 286.23 kg CO2e per thousand Euro.
This is due among other things to the tyre pressure measuring system installed on the premises at the end of 2011. This measures the tyre pressure of all trucks, buses and company cars, entering or leaving the site and reports this to the individual driver and the in-house workshop. This ensures that tyre pressure that is too low and leads to higher energy consumption, is quickly detected and eliminated.
In addition, the existing high-pressure mercury vapour lamps in the Grafschafter Logistics Center were replaced in 2012 with halogen metal halide lamps. Compared to the high-pressure mercury vapour lamps previously used, these have nearly twice as much light output and also pave the way to a high degree of energy efficiency. At the same time, motion detectors greatly minimise the energy consumption of the store in the company’s high bay warehouse.
Trucker initiative East Hesse
There is a lack of qualified professional drivers. Many companies want to train new recruits. But how do you attract young people to a job with an extremely bad image? How can we enhance respect for the profession?
To promote the future-proof benefits of this demanding profession more directly, and in an authentic a manner as possible, VTL draws on the shared commitment of companies anchored locally and regionally and is part of the Trucker Initiative East Hesse, launched by the Fuldaer Zeitung newspaper.
What is planned is a ten-part series in the Fuldaer Zeitung that will bring the profession of professional drivers from different angles to a public audience every week. The requirements for training to become a truck driver are a lot more than just getting a licence. They also involve state of the art technology, legal and social legislation, and dealing with customers. The aim is to present facts and stories related to the profession to increase its acceptance among those entering the labour market and their families and the general public.
Other activities like a Trucker Initiative information stand at the Autojournal-Autotag are designed to facilitate more direct dialogue with trucking companies, truck manufacturers, driving schools, and logistics companies.
“We see this commitment as a complement to the many important initiatives already existing nationwide”, explains Andreas Jäschke, Managing Director of VTL, who has first hand experience of the problems of the shortage of professional drivers among his system partners in the cargo alliance, “we believe that the undeservedly bad image of professional drivers can be improved if the authentic commitment of local actors is coordinated.”
Efficiency reserves identified
With cost pressure in the logistics sector increasing, it is also important for the CargoFamily to identify existing efficiency reserves. A term paper by logistics student Huib Claassen highlights possibilities of how, within the Fulda central hub, damage can be reduced, cycle times shortened, use of personnel and material can be optimised and loading times can be controlled and monitored.
VTL has been on a steady growth path since 2006, with the number of shipments up by 97% and turnover more than doubling. In the course of organic growth however, there was often insufficient time to implement internal process optimisation. As part of his studies at the University of Applied Science in Breda in Holland, student Huib Claassen examined areas in which there were efficiency reserves. What he found: VTL could modify various processes and turn them to a profit.
At 21, Huib Claassen is the holder of a truck driver’s licence and is already very familiar with logistical processes; because he has already worked for his father, Managing Director of VTL partner Claassen Logistics in Tilburg, in the warehouse, as well as in other areas and gained plenty of experience.
During his three-month placement at VTL, Claassen identified a total of four potential starting points: automated identification of pallets, reducing empty runs, optimisation of hub transport and the issue of operational controlling. Automated identification of pallets via radio-frequency-identification technology (RFID) is a big money saver for a start. The use of navigation software could prevent empty runs and drastically reduce paths at the Fulda central hub – according to Claassen, by at least 730 km a month. The logistics student also recommends evaluating existing data in a more targeted way and more promptly – and review existing processes on this basis. “Using a controller could make a significant contribution to solving existing challenges and promoting targeted process improvements”, underlines Claassen.
The VTL management will now examine if the proposals outlined can be implemented and at what cost.
Benelux is strong and green
According to a ProLogis study on the question of the most attractive economic areas for logistics companies in Europe, the Benelux area wins hands down. The survey found that some of the major success criteria are the proximity to customers and suppliers, availability of labour and flexibility of state institutions, quality and proximity of infrastructure. Good, if you are well-positioned here as a Europe-wide active cargo alliance and with a total of 11 partners, you have an equally dense network as in Germany.
This is also reflected in the numbers of the VTL network: 31 percent of European (non-German) shipments go to Benelux, 74 percent come from there. These amounts lead to daily traffic and good cooperation plus the definition of processes allows for standardised rates. Every partner drives to the central hub in Fulda or the regional West hub on a daily basis.
But it is not only economic aspects that are important in terms of cooperation, “Green logistics” is also a cross-border issue. Particular commitment has been shown here by the VTL partner De Rooy Transport in Houten: 3,000 trees have been planted in the company’s three-hectare forest to compensate for part of the CO2 emissions caused by transport. De Rooy has also been using an electric truck since July 2014 for deliveries in and around Utrecht, to play its part in further reducing emissions. Two other partners were able to prove with measures and action plans that they are able to meet the criteria of the Lean and Green Award, i.e. reducing CO2 emissions by 20 % within five years. The partner company Norbert Dentressangle Logistics in Welkenraedt will reduce its CO2 emissions by 20 percent within five years through driver training, hybrid technology, load optimisation and other measures, and received the Lean and Green Award for this. H. Veldhuizen Transport from Zaandam was awarded the same prize.
Partners in Benelux (A-Z):
Claassen Logistics – NL
CTS GROUP – NL
De Rooy Transport B.V. – NL
De Vreese Logistics NV – BE
EUROPA BELGIUM – BE
Jacob Meijer Forwarding B.V. – NL
Lentz Multimodal S.A. – LUX
Norbert Dentressangle – BE
H. Veldhuizen Transport B.V. – NL
Only feeding in:
Tiemex logistic services B.V. – NL
Van Duuren Districenters B.V. – NL
Sources:
http://lean-green.nl/en-gb/lean-and-green/what-is-lean-and-green/
http://www.die-logistik.de/13/29/prologis-umfrage-die-attraktivsten-logistikstandorte-europas/
http://www.logistik-heute.de/Logistik-News-Logistik-Nachrichten/Markt-News/10662/Umfrage-ermittelt-Europas-begehrteste-Logistikstandorte-Logistikstandorte-Ni
10 years Van Duuren Districenters
The Dutch transport provider Van Duuren Districenters is celebrating its tenth anniversary this year. Since the company was set up in 2004, Van Duuren has been able to boost its sales tenfold.
“We have developed from a small family business to a serious competitor to the large carriers”, emphasises Managing Director Jeroen van Duuren. After all, van Duuren offers its customers tailor-made solutions and undivided attention. “Short communication channels and personal contact with the customer are self-evident for us and this is something large transport companies usually can’t offer”, says van Duuren. This is one of the main reasons the logistics provider headquartered in Vianen in Holland has recorded significant growth rates year on year even during the credit crunch.
Another success factor is how the company is seamlessly integrated into an extensive, high-quality pan- European transport network. “We work with a number of partners, who are all specialists in their respective fields. We have visited these partners in person to see if their modus operandi meets our quality requirements”, emphasises CEO Jasper van Duuren. That is how you can work with great flexibility and in a customer-focused way.
In the future, the service provider wants to further expand its business mainly in the former Eastern bloc countries and further raise its sales organisation’s awareness of customer needs and wishes. This will involve improving the processes within the organisation and quickly setting up the new transport management system. “By providing our employees with ongoing training and development, we ensure the quality of our services is continually improved. That for me is one of the most beautiful aspects of entrepreneurship”, says the shipping boss.
The van Duuren brothers are also facing the future challenges in the industry with optimism – and not without reason. The company is for example responding to the growing skills shortage with an innovative concept: the special Van Duuren Logistics Bachelor award is designed to inspire more young people to go for a career in logistics.
PLA - a new look at part load segment
Geo data rather than post codes – with this approach the newly formed Part Load Alliance (PLA) wants to revolutionise the part load segment. The benefit: using a user-friendly online portal, PLA partners can now immediately plan their part loads a lot more easily and process them a lot more cost-effectively.
Whether it is general cargo or part loads, dispatchers need the support of innovative IT for optimum utilisation and the avoidance of empty runs. VTL uses software solutions from the company itRessort, which has developed the partner portal myVTL.de. itRessort is very familiar with the complex requirements of a general cargo network and has built on this experience to create a solution for cross-partner route optimisation of partial loads – and uses these geo-coordinates instead of post codes.
This innovative solution is used exclusively by the new Part Load Alliance (PLA), formed by the VTL partner Hintzen Logistik. Other VTL members are also involved. The optimisation procedure based on geo-coordinates means part loads can now be planned more easily and processed a lot more cost-effectively, traced using Tracking & Tracing – and the estimated time of arrival at the receiver’s premises is also given, an innovative customer service, creating market opportunities for PLA members.
As a member of the PLA, medium-sized carriers with their own fleet can in the future enter requests via a part load batch in the web portal. The software then checks all options and focuses in particular on the optimum utilisation of the trucks. Requests, including the cost incurred in each case, can be answered immediately.
The efficiency of transport is of course always top priority. As a result, in part load transport, PLA completely forgoes central handling and right angle traffic and expensive detours. And the problem of empty runs is also reduced. While 36 % of all trucks are currently empty on German motorways, the new IT-based scheduling can bundle part loads of all system partners relationally onto the respective lines – this creates significant cost benefits and protects the environment.
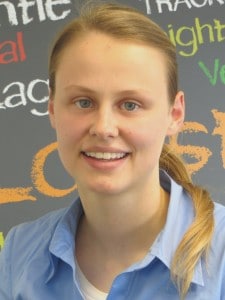
Theresa Füller (22) completed her exam as Freight Forwarding and Logistics Services Manager after 2.5 years this spring. She was taken on by VTL and has since been responsible for the Key Accounts Department. In autumn, she will be starting her dual studies and will hand on the baton to Anna-Maria Bösel (21), who has just passed her Chamber of Commerce final exam as a Freight Forwarding and Logistics Services Manager and was given the best student of the year award by school.